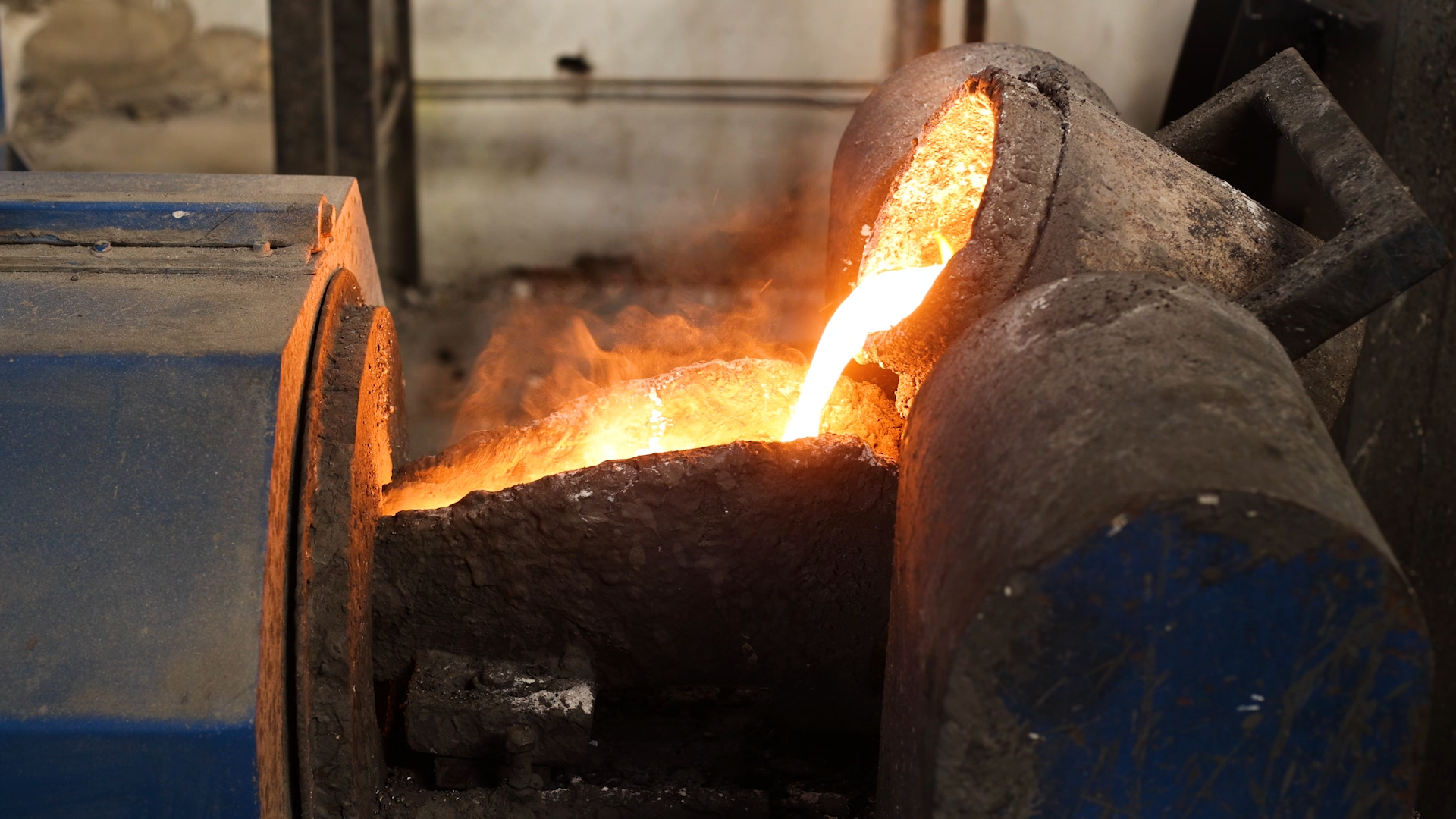
Centrifugal Casting
How Does Centrifugal Casting Work?
Centrifugal casting is a metal casting technique in which a metal is poured into a mold and the centrifugal force aids in the formation of a hollow structure. Metal is heated to a molten state, and this is poured on a spinning mold; this causes the metal to stick to the inner face of the mold creating the desired shape. This process is especially useful for making cylindrical parts of a space or with the same thickness of walls.
Advantages of Centrifugal Casting
- Superior Mechanical Properties: Centrifugal casting has the advantages of fine-grained structure, higher mechanical strength, longer service life, and better corrosion resistance.
- Consistent Wall Thickness: The control of the centrifugal force is critical in the creation of the wall thickness of the components since it is consistent.
- Improved Material Utilization: Less wastage of materials as compared to the other casting methods which is attributed to high metal flow.
- Cost-Effective: It also means high production rates and reduced amount of machining that results in lower costs.
Applications of Centrifugal Casting
Centrifugal casting finds wide applications in various industries, including:
- Automotive: Brake drums, rotors, axle shafts, and cylinder liners.
- Aerospace: Engine parts, blading for turbines as well as structural items.
- Oil and Gas: Valves, Pipe fittings, and different parts of a pump.
- Power Generation: Turbine shaft, impellers, and casing.
- Other Industries: Rollers, bushes, and sleeves.
Types of Centrifugal Casting
There are primarily two types of centrifugal casting:
- True Centrifugal Casting: Metal is poured into a rotating mold, and through the force that rotates the mold, the metal fuses itself to the wall of the mold hence taking the shape of the molds.
- Semi-Centrifugal Casting: In this process, the mold cavity is filled with a pre-formed metal core, and molten metal is poured on top of it. The centrifugal force also throws the metal in equal proportion to the core as well as the mold.
Centrifugal Casting Process
The centrifugal casting process typically involves the following steps:
- Mold Preparation: The mold has to be cleaned, coated, and assembled.
- Melting: The required metal alloy is then melted in a furnace.
- Pouring: The mold rotates, and the molten metal is then introduced into the mold.
- Solidification: The metal undergoes a process of solidification due to the effect of Centrifugal Force.
- Cooling: After the casting is done, it is cooled slowly to minimize the effects of thermal stresses.
- Machining (if required): The final finishing and machining are done to bring the size of the piece to the required size and accuracy.
Challenges and Considerations
While centrifugal casting offers numerous advantages, it also presents certain challenges:
- Mold Design: The major challenge with complex shapes is that it is often hard to do.
- Metal Selection: Only certain metals are suitable to be used in centrifugal casting.
- Process Control: It will also require close control of the rotational speed and the temperature at which the molten metal is poured.
Centrifugal casting is an effective and versatile manufacturing technique that can generate consistent parts made of metals with uniform characteristics. Some of the common uses include making it a popular choice due to its versatility and affordability.
Industries We serve
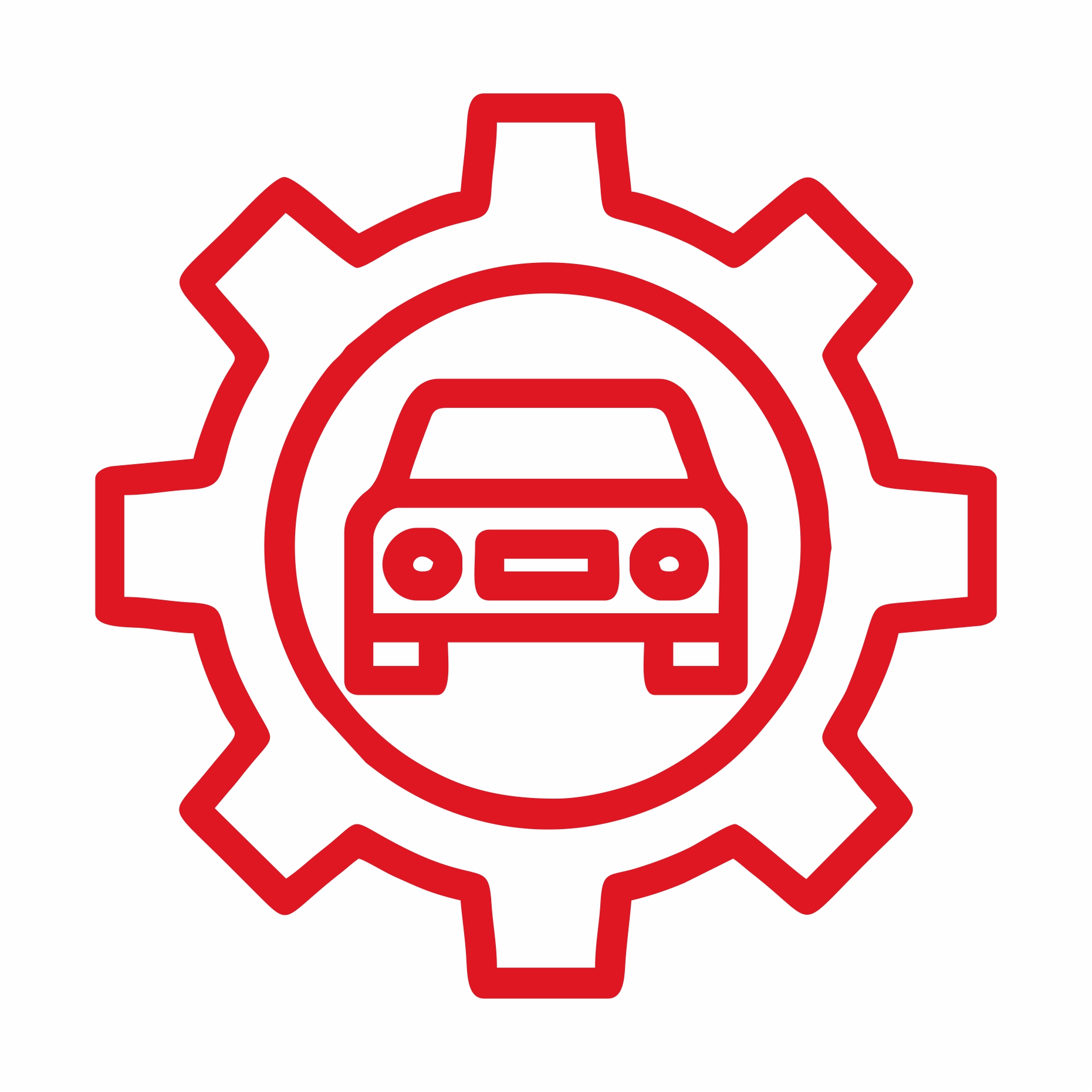
Automobile Industry
The automobile industry relies heavily on custom-made casting parts for its functionality and innovation. These parts, created using molds for intricate shapes, are essential for engines, transmissions, and other core components.
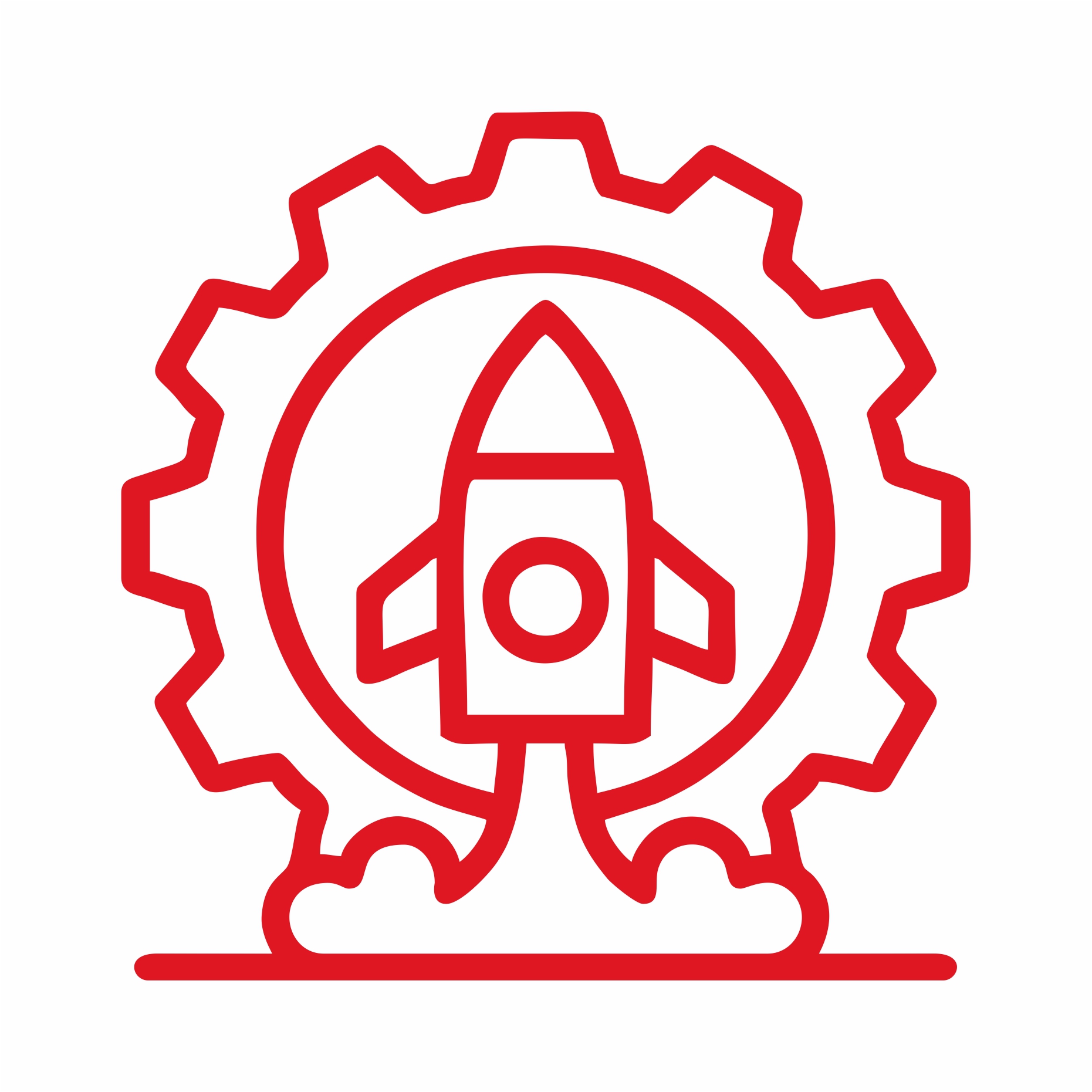
Aerospace Industry
Custom-made casting parts are the backbone of the high-tech aerospace industry. Their ability to take complex shapes makes them ideal for crafting lightweight yet strong airframes, jet engine components, and other critical structures within aircraft.
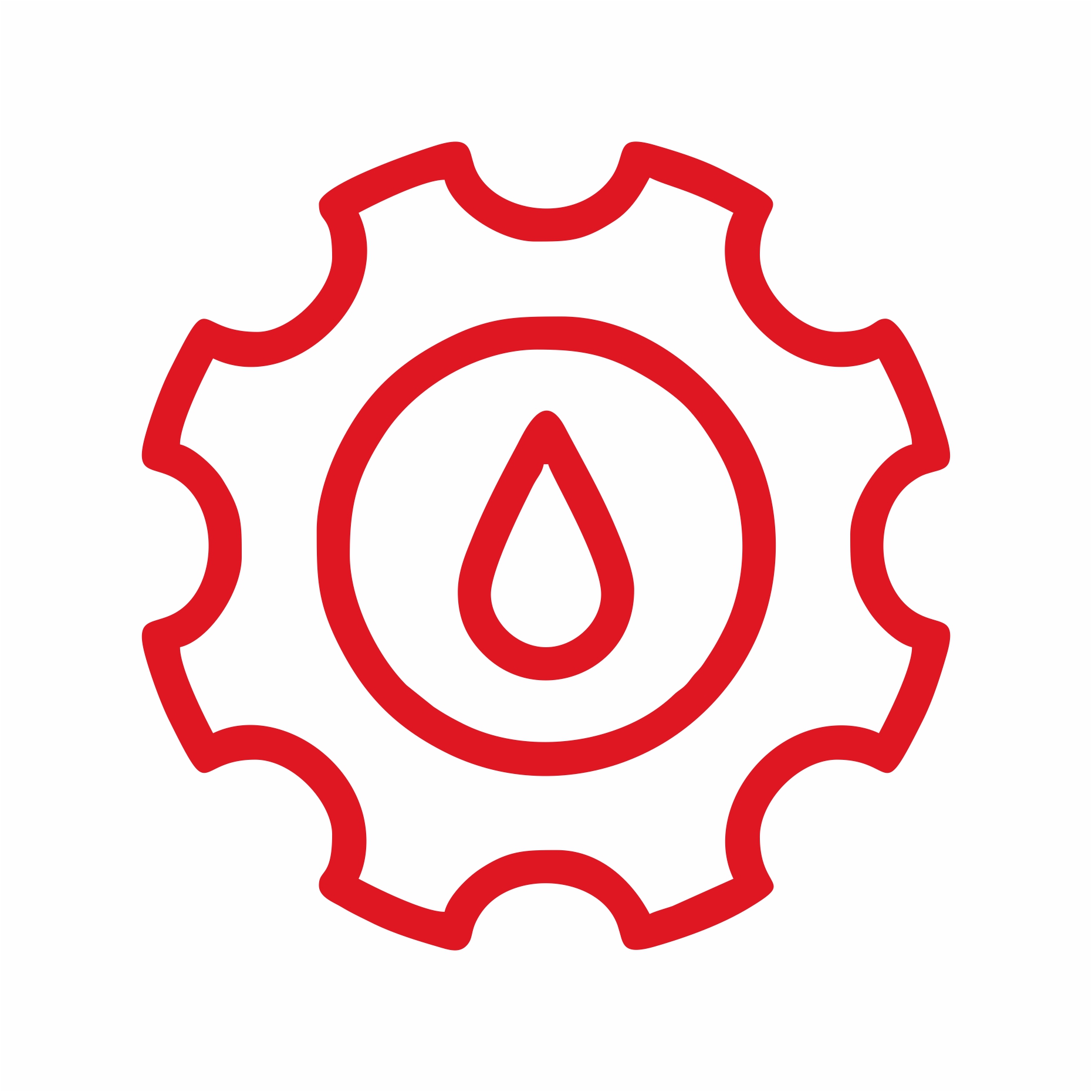
Oil And Gas Industry
This industry is growing rapidly. We have used alloys to manufacture our custom made casting parts. It provides strength and corrosion resistance to valves, pumps and wallheads.