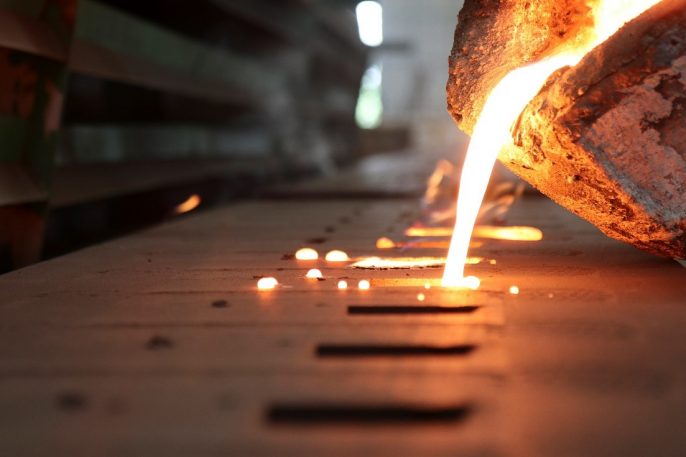
Green sand casting
Green sand casting is one of the oldest and most versatile metal casting methods that has been in use for a long time now. It entails preparing a mold from green sand, which is sand that has been mixed with water and a bonding material. Molten metal is then poured into the mold to cast the required shape.
The Green Sand Casting Process
- Pattern Making: An actual product is made using wood, metal or plastic replicate similar to the pattern intended for the final product.
- Mold Preparation: The pattern is laid in a sand mold box and then force is applied to make the impression on the box. Sand is washed with water and a binder to impart strength to it.
- Molding: Sand is packed into the mold box and the pattern is withdrawn leaving a negative impression of the desired product.
- Core Making: If the casting has internal recesses, then sand cores are prepared and introduced into the mold cavity.
- Pouring: The molten metal is then introduced into the mold cavity where it fills the space up to the pattern.
- Cooling and Solidification: Molten metal is poured into the mold and allowed to cool and solidify.
- Shakeout: The metal casting is taken out of the sand mold after it has been solidified.
- Cleaning: Sand and any other unwanted material on the casting is removed from it.
- Finishing: The casting also goes through some other processes such as grinding, machining, or heat treatment in order to obtain the right dimension and properties.
Advantages of Green Sand Casting
- Versatility: This is well suited for a larger variety of metals and intricate forms and cross sections.
- Cost-effective: Low cost of equipment and materials as compared with other methods or forms of construction.
- Good surface finish: Provides satisfactory surface finish without subsequent polishing.
- Rapid production: These are suitable for printing small and large volumes of the product.
Challenges and Concerns of Green Sand Casting
- Dimensional accuracy: Higher surface roughness than other forms of casting processes.
- Environmental impact: The disposal of sand can be a problem from the environmental point of view.
- Labor-intensive: Complex as it demands a skilled workforce in the formation of mold and also the casting process.
Applications of Green Sand Casting
Green sand casting is widely used in various industries, including:
- Automotive
- Construction
- Agriculture
- Machinery
- Plumbing
Environmental Considerations
Although green sand casting can be applied to various casting processes, its effect on the environment should not be overlooked. However, significant measures should be taken to ensure proper management of sand reclamation and recycling systems to reduce impacts on the environment.
Green sand casting continues to be a basic procedure in metal casting today because of its simplicity, low cost, and effectiveness. However, the use of technology and growing environmental consciousness increases the use of other casting processes.
Industries We serve
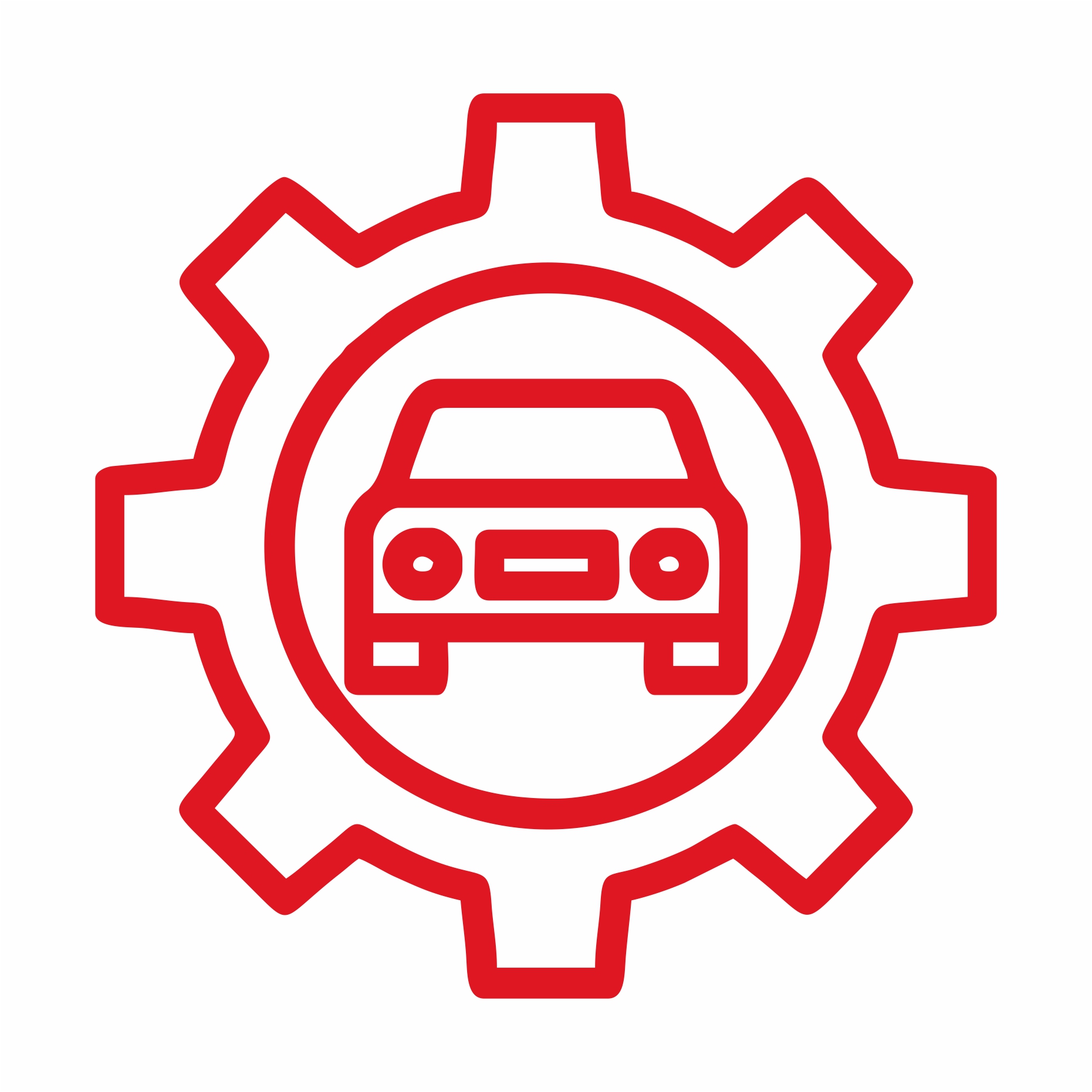
Automobile Industry
The automobile industry relies heavily on custom-made casting parts for its functionality and innovation. These parts, created using molds for intricate shapes, are essential for engines, transmissions, and other core components.
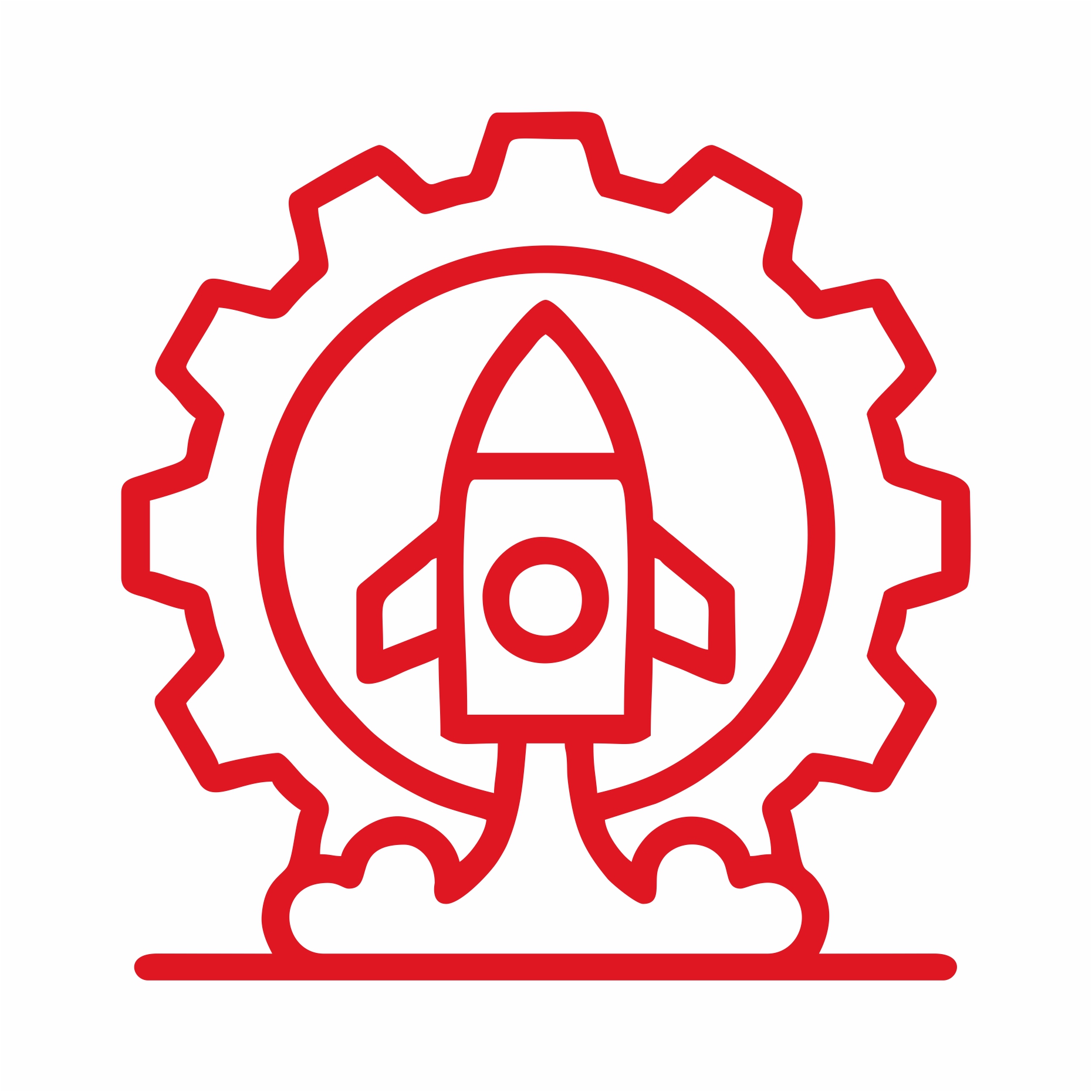
Aerospace Industry
Custom-made casting parts are the backbone of the high-tech aerospace industry. Their ability to take complex shapes makes them ideal for crafting lightweight yet strong airframes, jet engine components, and other critical structures within aircraft.
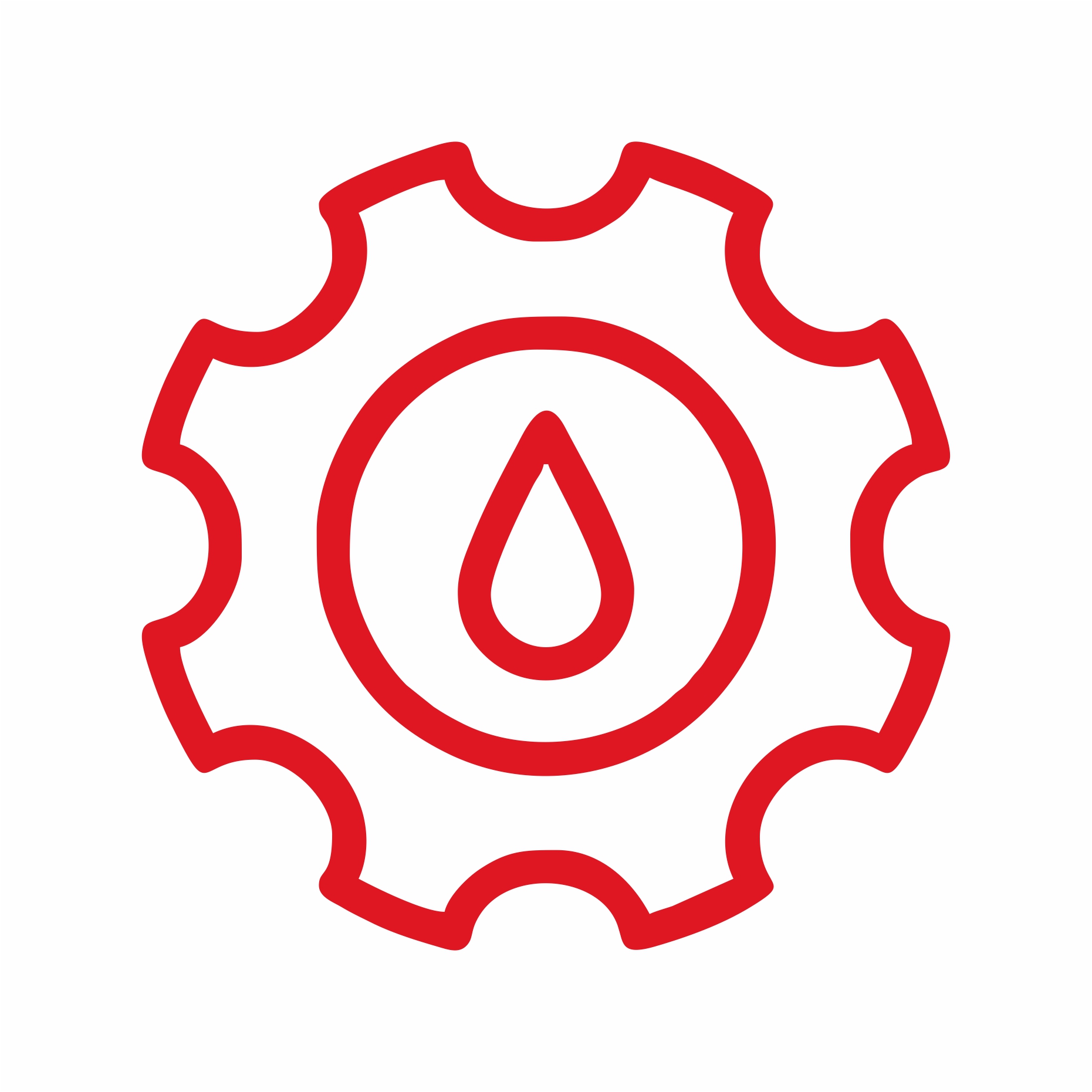
Oil And Gas Industry
This industry is growing rapidly. We have used alloys to manufacture our custom made casting parts. It provides strength and corrosion resistance to valves, pumps and wallheads.