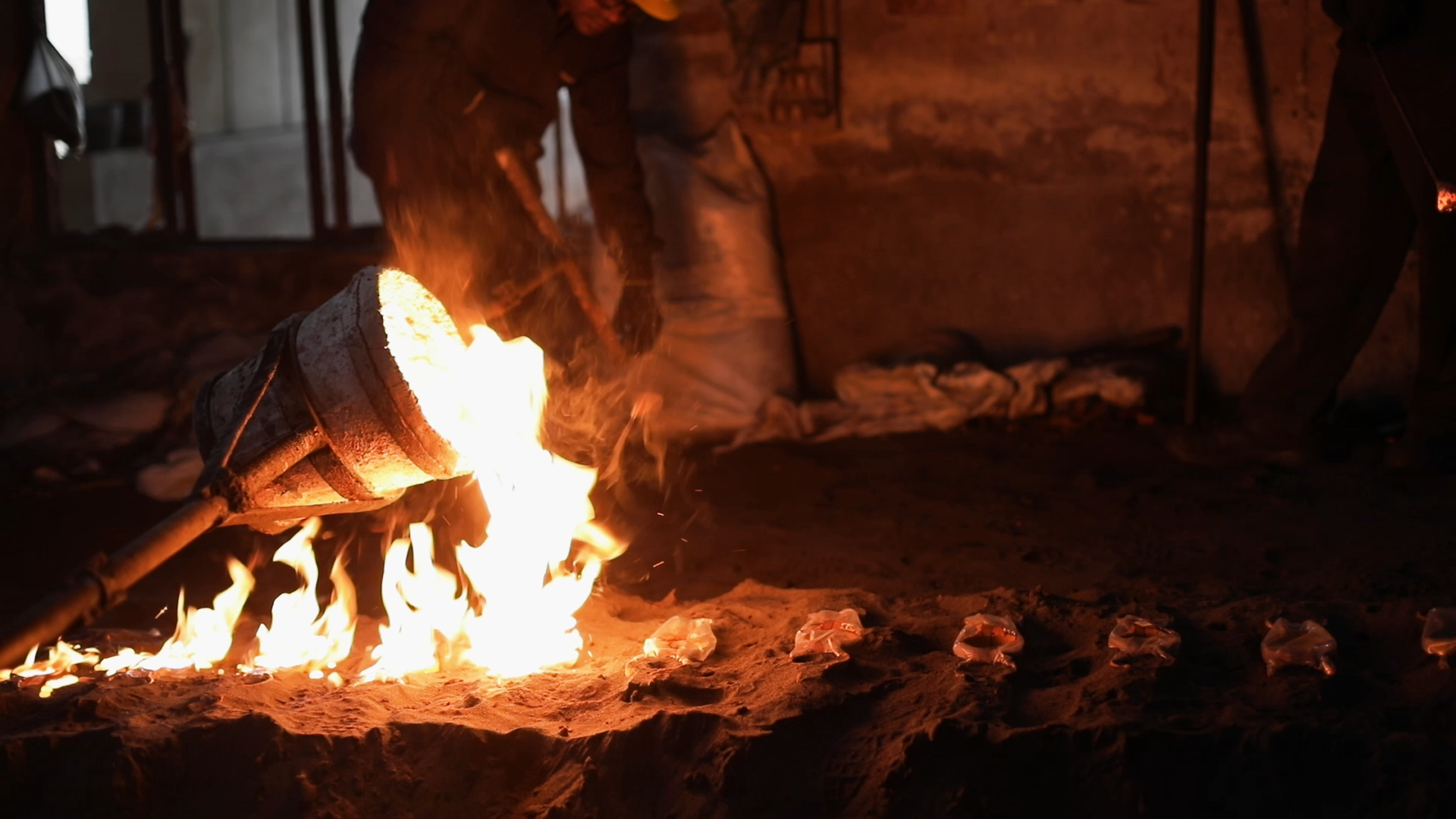
Shell Mould Casting
Shell molding is an investment casting process that is used in the production of high-precision castings accompanied by excellent surface finish and accuracy. This process involves placing on a wax or plastic pattern a thin ceramic shell which, when filled with molten metal, produces the casting.
The Shell Moulding Process
- Pattern Preparation: An outline of metal is formed; this will be the configuration to be used to cast.
- Shell Formation: After the creation of the metal pattern, a heated resin-coated sand is packed into it to form a very thin and consistent shell.
- Curing: The shell is then treated to help make it rigid.
- Pattern Removal: Upon the shell’s hardening, the metal pattern is then taken out from it.
- Metal Pouring: In this process, the molten metal is poured into the shell cavity in still a molten state.
- Cooling and Solidification: The metal cools off and matures within the shell portion.
- Shell Removal: The gating system is finally taken out and the solidified casting is retained in the shell.
- Cleaning and Finishing: The casting is cleaned and finished according to the required standards.
Advantages of Shell Mould Casting
- Excellent Surface Finish: Creates castings with a very fine surface finish.
- High Dimensional Accuracy: Provides for accurate dimensions and controlling of tolerances.
- Complex Shapes: It can make highly complex and realistic castings.
- Rapid Production: Tends to produce parts relatively quickly compared to other casting methods.
- Less Waste: How it works: It creates a small amount of waste during the process.
Applications of Shell Mould Casting
Shell molding is utilized in numerous industries and offers certain advantages, which is why it is popular among others. Some common applications include:
- Automotive components
- Machinery parts
- Plumbing fixtures
- Pump and valve bodies
- Aerospace components
Challenges and Concerns
While shell molding offers numerous advantages, it also presents certain challenges:
- Pattern Cost: Metal patterns can be costly in manufacturing.
- Shell Strength: The shell must also be adequately constructed to accommodate the pouring of molten metal.
- Environmental Impact: The process utilises resins and chemicals – and correct handling and disposal are essential
Future Trends in Shell Moulding
While shell molding offers numerous advantages, it also presents certain challenges:
- Automation: Growing the scale of automation to bring efficiency to a new level.
- New Resin Systems: High-performance, environmentally friendly formulations of resin systems.
- Digital Pattern Making: The applications of 3D printing technology and digital means for pattern generation.
Shell molding is among the most important casting processes that exhibit high-quality standards, precision, and productivity. Consequently, it is a versatile material that is capable of molding intricate shapes, due to its widespread use in various industries.
Industries We serve
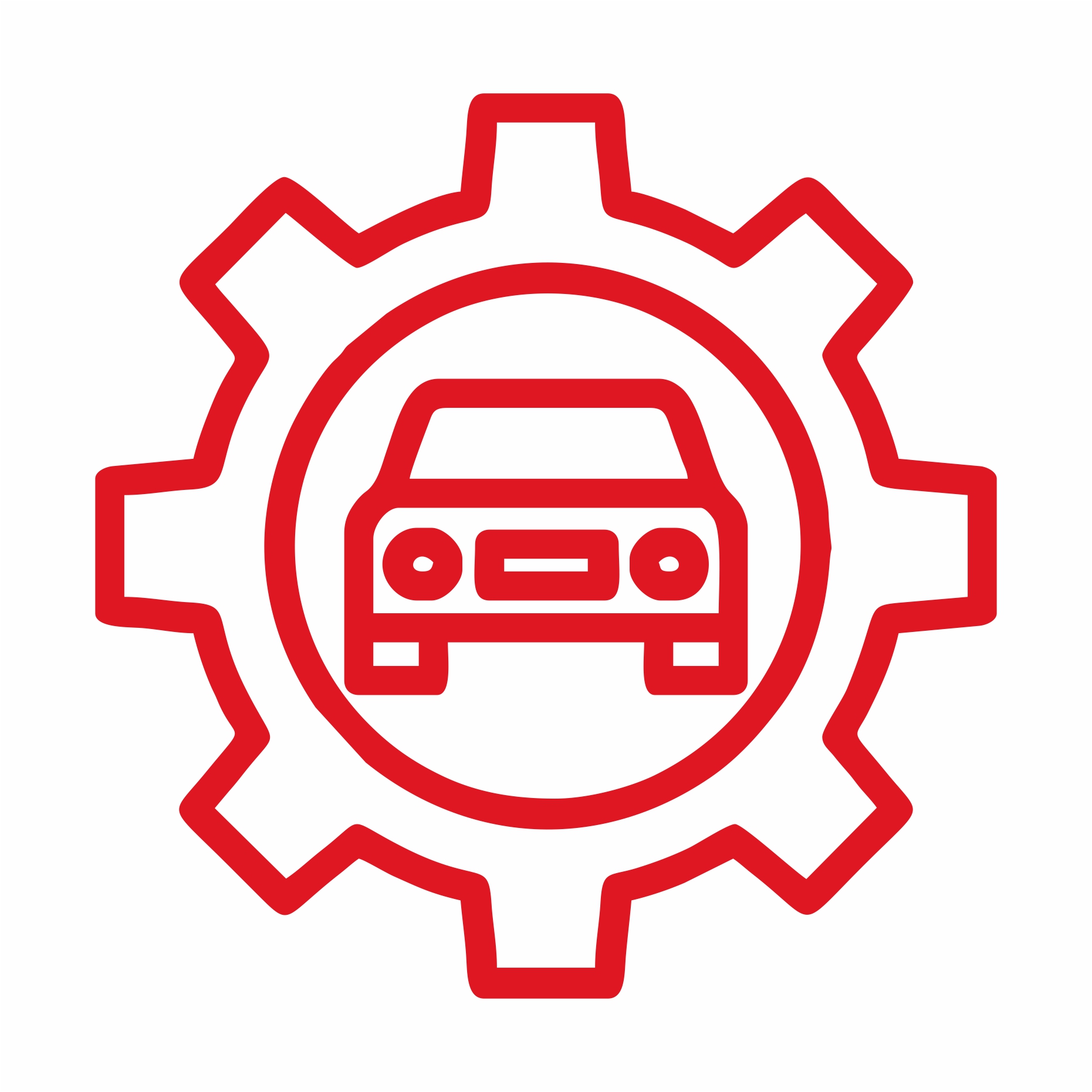
Automobile Industry
The automobile industry relies heavily on custom-made casting parts for its functionality and innovation. These parts, created using molds for intricate shapes, are essential for engines, transmissions, and other core components.
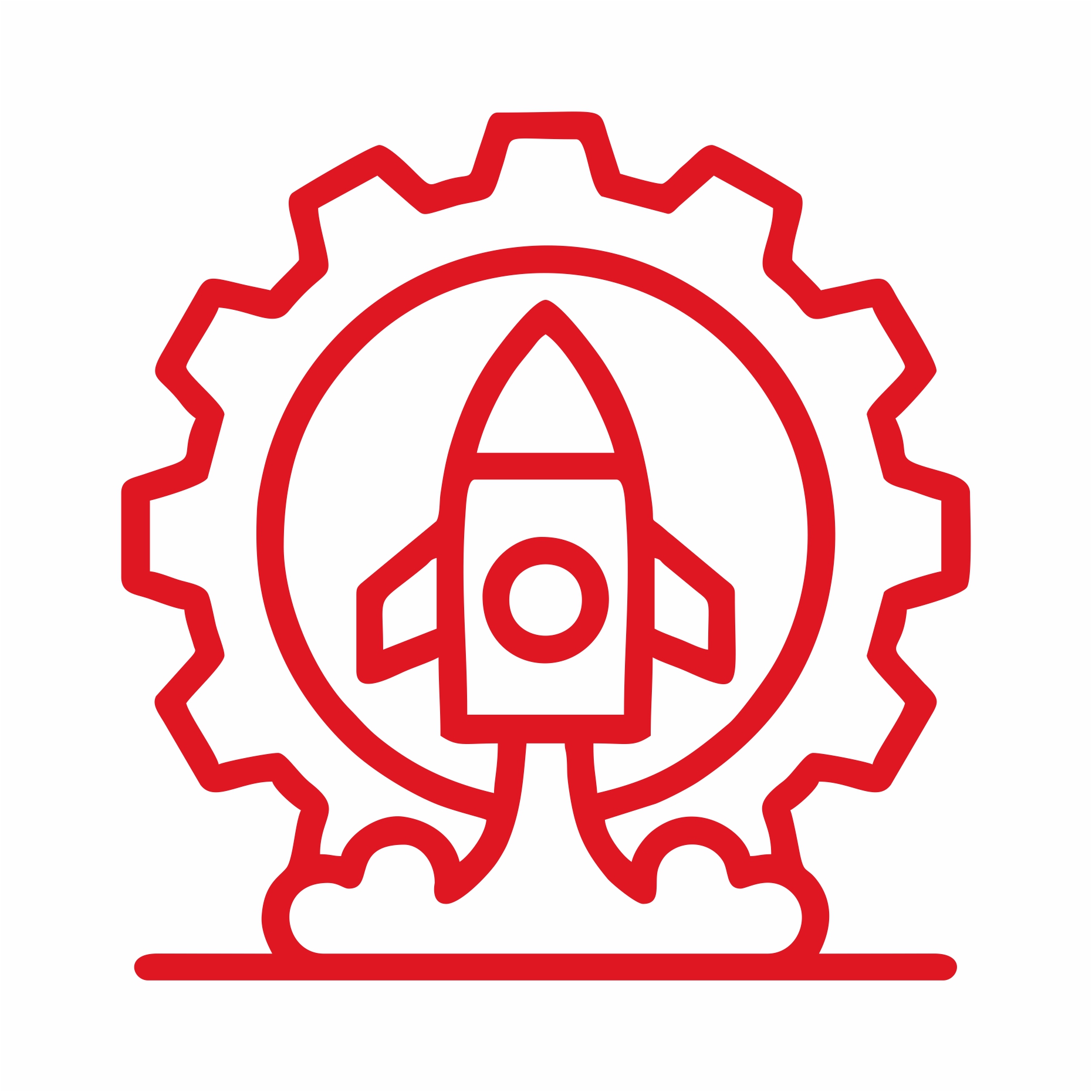
Aerospace Industry
Custom-made casting parts are the backbone of the high-tech aerospace industry. Their ability to take complex shapes makes them ideal for crafting lightweight yet strong airframes, jet engine components, and other critical structures within aircraft.
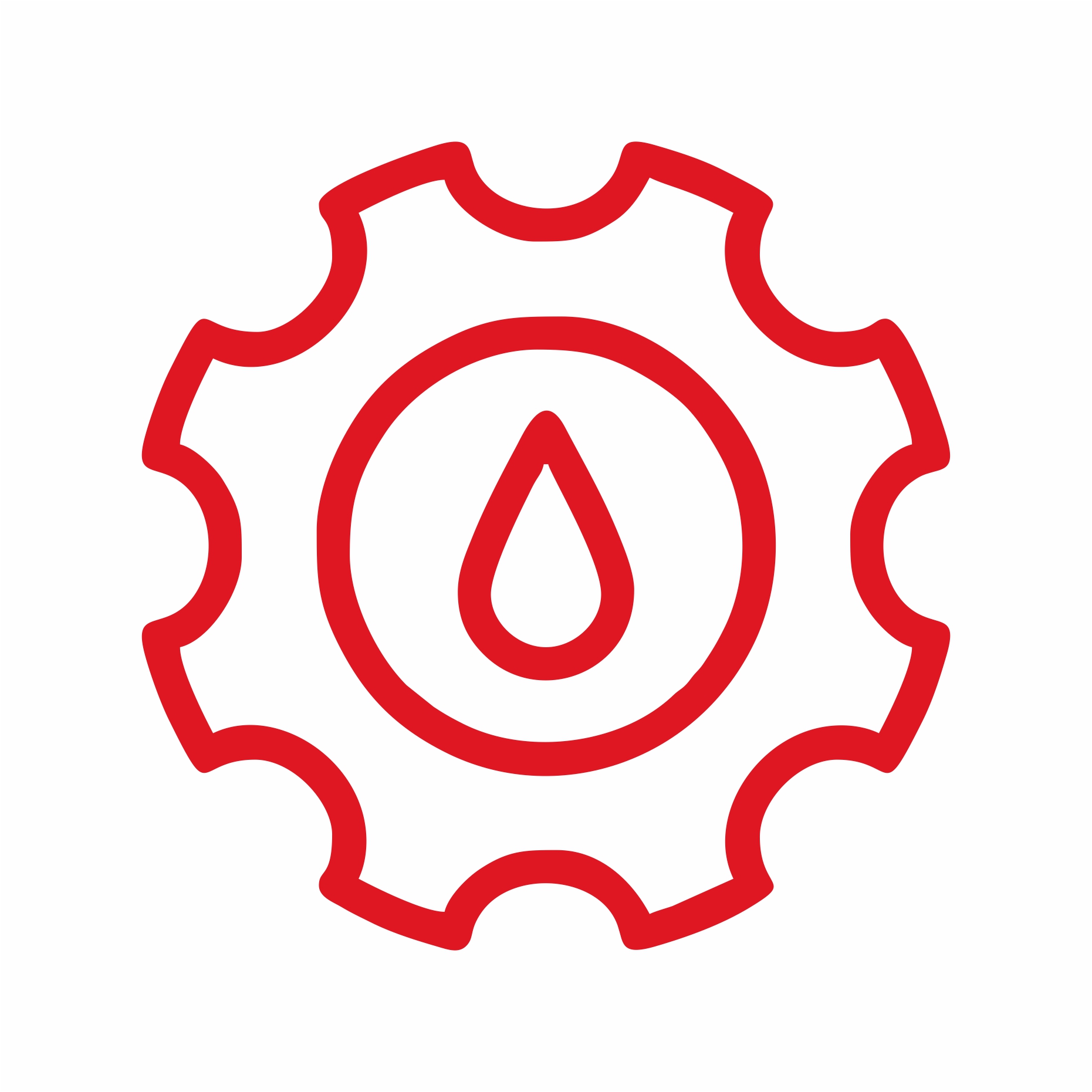
Oil And Gas Industry
This industry is growing rapidly. We have used alloys to manufacture our custom made casting parts. It provides strength and corrosion resistance to valves, pumps and wallheads.